The industry came together to cheer for the champions who made a difference in whatever services they offer
At one of the finest ballrooms of the Lalit in Mumbai, a ceremony was held unlike any other in the city. It was the evening of 7th September when the shipping greats came together for the glitzy Gateway Awards night. The maritime and logistics community from all over the country came dressed in their finest best of greys and blues and the growing tribe of ladies in the shipping business painted the hall with their bright hues. This was the evening the industry chose to celebrate with their colleagues and peers for carrying the industry through successfully for another year.
Representatives of shipping lines, ports, CFSs, ICDs and logistics companies cheered for the champions who through their perseverance pushed the boundaries in everything from customer service, new products to using technology to disrupt the way business is done. It was a night where the industry stood up together to celebrate excellence, innovation and best practice across the sector.
About 15 categories were enlisted and all Indian maritime companies were invited to nominate their business entities for evaluation by the Gateway Awards Jury. The parameters for business growth that were considered for shortlisting were volume growth, asset growth, productivity parameters, and the main efficiency indicators considered were capacity utilisation, turnaround time and dwell time of vessels. The other main indicators to net awards were innovation and investment to improve customer service, improvement in connectivity to ports and container freight stations. Through a detailed jury process, data received from the nominees was provided to the jury committee for review and collation. The panel then discussed the evaluation criteria based on the ground rules and the winner was selected on the jury member voting individually.
The recipients accepted these awards to a thunderous applause and many a standing ovation. Once the awards were given and just when everyone thought it was over, one person made a grand entry and elevated the level of the awards ceremony a notch higher. Former Indian Cricket Team Captain and ace baller, Kapil Dev walked on the red carpet and the majesty of his persona added the glitz to the ceremony. As he took to the stage, the gathering cheered loudly for their star cricketer as he inspired one and all through his gritty comments.
The awards evening may now be over but our Gateway Awardees will be justly entitled to bask in the glow of their success for the next 12 months until their peers up the benchmark higher to qualify and bag next years’ awards. A terrific night of celebration marked out a superb set of winners. Maritime Gateway congratulates them all and thanks everyone who entered.
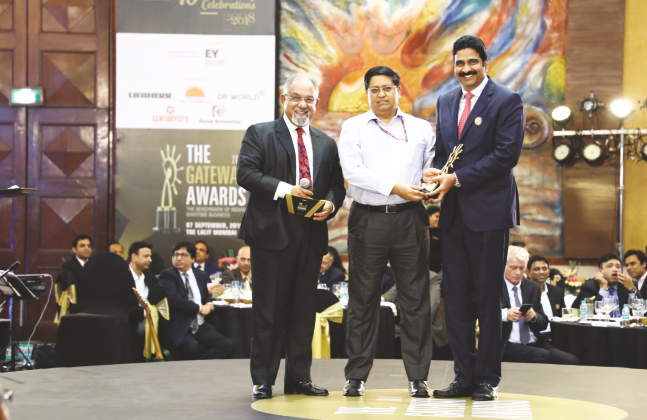
The fastest growing private port on the east coast of India, Krishnapatnam Port has bagged the ‘Bulk Port of the Year’ award for the second consecutive year. So what has enabled this largest port on the horizon to continuously raise the performance bar higher? And the answer is in the throughput the port has recorded in FY-2017- 18: 34.83 million tonnes of dry bulk, 1.28 million tonnes of break bulk and 1.63 million tonnes of liquid cargo has been handled by the port during the assessment period, which brings the port far ahead of the competition. With an installed capacity of 67.5 million metric tonnes the port has recorded a growth rate of 25.37 per cent in FY2017-18 over FY2016-17.
With a capacity utilisation of 52.48 per cent, Krishnapatnam Port has recorded performance indicators which prove it to be better than the best. Disposal of bulk cargo is often a time consuming process, but the port has managed to maintain its lead with average turnaround time of 4 days and average pre-berthing detention time of 2 days. This has been made possible with the highly automated and mechanised processes implemented at the port for both loading and unloading of bulk cargo, which has also enabled the port to expedite the average output per ship berth day that stood at 30,000 metric tonnes during the assessment period. The port has recorded 20 per cent growth in average output per ship berth day in FY2017-18 over FY 2016-17 in million tonnes.
The port has installed 3800 metres of new belt conveyor system to expedite the unloading of bulk cargo with zero wastage. New stacker reclaimer and reclaimers have been installed at the port to expedite disposal of cargo. Another infrastructure addition that adds speed to movement of bulk cargo is installation of two rapid wagon loading stations. An automated fertiliser handling system is another attraction that makes unloading and bagging of imported fertilizer quick and easy. With growing business the port has been conscious to expand its connectivity with the addition of a new railway line to Obulavaripalle which is on the verge of completion and due to be commissioned in early 2018-19.
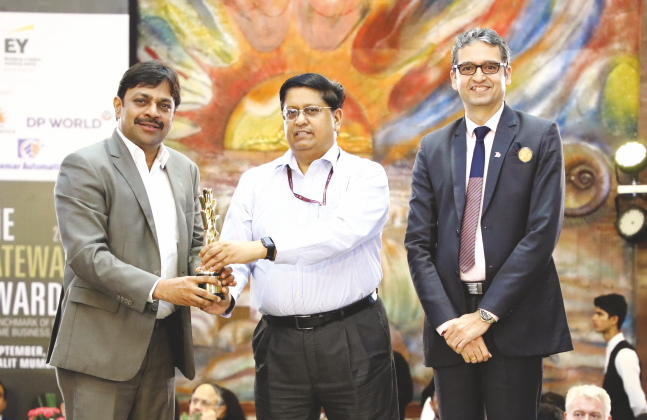
The winner of this award could be anybody’s guess as it is none other than JNPT to handle the major chunk of India’s containerised trade. This India’s busiest container handling port edged ahead of its competition to grab the award with its remarkable performance indicators which include capacity utilisation of 90 per cent and average turnaround time of 1.30 days which boasts of the operational speed of the equipment at the quay. Another feature worth noticing is the average pre-berthing detention time that stands at 2.88 hours, pointing at the swift operations at all the terminals of the port. The productivity at this major port can be gauged by the average output per ship berth day that stands at an astounding 31,516 tonnes. Y-o-Y growth in average output per ship berth day is 1.5 per cent in FY 2017-18 over FY2016-17. The average crane productivity of 23 moves per hour is a reflection of the state of the art equipment used at the port.
A major contributor to this tremendous upbeat in the performance of the port is the commissioning of the 4th container terminal with three berths. On the equipment side, the 15 new e-RTGCs added at the port are electrically powered, cost economical with minimal maintenance and environment friendly. They have 2-twin twenty container handling mechanism with 50MT capacity under spreader. This new machinery has provided the required thrust to propel the efficiency of the port to new heights. The intermodal lifts at the port increased 2 percentage points in August 2018 to a record 16.8 per cent share, up from 14.7 per cent in July. A significant achievement of the port is the rise in rail movement of cargo and drop in road movement. In August 2018, import/export movement of containers by rail totalled 69,978 teu, out of the 417,360 teu handled at the port during the month. The share of road cargo movement decreased from 85 per cent in July to 82.5 per cent in August.
JNPT is well connected to the hinterland via rail network through its 2 track connectivity from Panvel. Indian Railways has commenced work on Western Dedicated Freight Corridor from Delhi to JNPT.
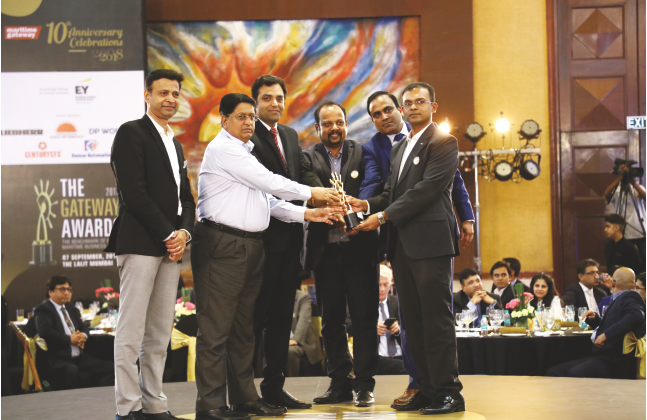
Creating capacity ahead of demand’ is the winning formula of Krishnapatnam Port Container Terminal that has fetched it laurels to bag the ‘Container Terminal of the Year’ award in the ‘Below 0.6 million teus’ category. The terminal has moved a remarkable 2,23,000 teus in imports and 2,56,552 teus in exports, including transhipment, during the assessment period. The terminal also leads in moving transhipment cargo on the east coast with volumes of 2,12,466 teus transhipped in FY2017-18.
With an installed capacity of 1.2 million teus the terminal has always been in the forefront for promoting the government’s vision to increase movement of cargo through the coastal route. During FY2017-18 the terminal has moved 19,518 teus of coastal cargo. Congestion is a word much unheard at Krishnapatnam Port Container Terminal as it has abundant yard area space of 36 hectares and an ambitious plan to increase capacity to 4.8 million teus. Even with the tremendous increase in the volumes of containers moving in and out of the port, it has a capacity utilisation of mere 35 per cent. The state-of-theart equipment used at the terminal has maintained average turnaround time at a minimum of 6 days.
The terminal has maintained a history of fastest loading and unloading of cargo onto vessels, which has made it a favourite destination for calling by shipping lines, as the average pre-berthing detention time is a negligible 1.25 hours. The ship captains have never found their vessels stay longer at the terminals as the average output per ship berth day is maintained at an enviable 26,128 tonnes. The terminal has posted a tremendous 84.61 per cent growth in average output per ship berth day during the assessment period.
The terminal often bets on the efficiency of its state-of-theart infrastructure defined by the average crane productivity maintained at 32.78 moves per hour. The productivity has increased by 14.86 per cent in FY2017-18 over FY2016-17.
Krishnapatnam Port Container Terminal has expanded its infrastructure during the assessment period by installing 16 reach stackers, 4 RTGCs, 5 quay cranes, 13 forklifts and 2 hydra.

If recording a throughput of 10,89,155 teus is a remarkable feat, then DP World – Mundra International Container Terminal definitely deserves to be awarded the Container Terminal of the Year award, in the above 0.6mill teus category. The terminal boasts of moving 499,708 teu in imports and 579,599 teus in exports during the assessment period of FY2017-18. Not to stay behind in transhipment, the terminal has recorded 9 per cent increase in transhipment over FY2016-17. Having an already installed capacity of 1300,000 teus, the terminal has further added 200,000 teus capacity to meet the growing demand of exim traffic moving through the port. The capacity addition is supported with installation of new equipment: A new Quay Crane and a Rail Mounted Gantry Crane have been added to further enhance terminal productivity and augment automation at the port. The new Quay crane is a super post panama with outreach of 60 meters, twin lift and is equipped with latest technology, capable of handling next-generation large size vessels. It comes with a Remote Crane Management System (RCMS), which aids superior planning of maintenance, thereby minimising downtime.
The equipment (both Quay Crane and Rail Mounted Gantry Crane) are designed for remote control operation, which will enhance operational efficiencies, thus improving productivity, whilst ensuring improved safety standards at the same time. With reduced engine maintenance, the advanced technology to automate and remotely operate a Rail Mounted Gantry crane is a first in India. To facilitate the trade, a vast 25 hectares of yard area has been provided for storing containers. Responding to the demand by trade the terminal has added Protea Service of Maersk Line Africa and IAGX service of Tehama to Upper Gulf.
Highlighting the efficiency of the terminal is the average vessel turnaround time of just 0.85 days or 18 hours. The average pre-berthing detention time is maintained to a minimum of 2.17 hours, which is a big relief to the shipping lines calling the terminal. Vessels arriving laden with cargo are disposed quickly with average productivity of 32.85 moves per hour.

The Danish shipping goliath has just grown bigger over the years. With 22 direct services to India connecting 17 ports on either coasts and a huge volume of 21,16,005 teus handled in FY2017-18, Maersk Line India Pvt Ltd clearly stood tall among its competitors, to claim the ‘Container Liner of the Year Award.’ Maersk has been making rounds in the news recently for its various initiatives – be it digitalisation or capital funding for SMEs.
Some of its initiatives worth a mention are: Remote Container Management (RCM) that provides real-time visibility on temperature, humidity and ventilation settings of the containers. This service has taken off quite well in India with more than 150 customer sign ups. Maersk is well ahead in understanding and offering cold specialized services and is currently catering for the Indian growing market demand.
Efforts to digitize the customer experience with services like online quote, book, submit shipping instructions, print Bill of Lading, get delivery order, download invoices, make payments. etc have made it possible to interact digitally with customers throughout the process thus saving time and effort.
To further digitise and enhance the user experience, a new division called global trade digitisation has been started where Maersk will partner with supply chain actors, including authorities, on how to digitise supply chain interactions. New age payment solution called Smartpay has been introduced to simplify the payment process and reduce time taken from 2 days to instant online payment, which gives customers the B/L’s immediately.
In compliance with IMO’s decision to ban high sulphur fuels by 2020. Maersk plans to replace bunker fuel with fuels with lower sulphur content thus complying with the global regulations set.
Piloted in India, Maersk Trade Finance, now operating in six countries, will offer post shipment export finance solutions in India and since 2017, has disbursed over $100 million to its customers here. In the next 12 months, Maersk will lend another $200 million to Indian businesses.
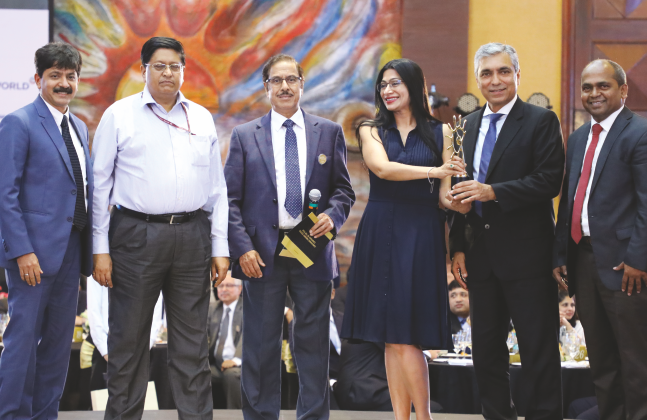
Allcargo Logistics has emerged as not just one of India’s largest integrated logistics solutions provider in the private sector, but is also a global leader in the LCL (less than container load) segment of the nvocc services business. The company recently showed its prowess in 2005 when it acquired Belgium-based ECU Worldwide, a company five-times its own size. Today Allcargo has its footprint in over 160 countries, with a strong network of more than 300 offices. The company globally employs over 3,500 people.
Going by the performance indicators Allcargo Logistics recorded a combined throughput of 2,93,817 teus in FY2017-18, which marks a growth of 4 per cent over the previous year. Major export commodities moved by Allcargo include garments, pharmaceuticals, industrial goods, machineries, project cargo, chemicals and handicrafts. Major imports include chemicals, dyes and intermediates, fruits, pharmaceuticals, machineries, project cargo, cosmetics, consumer goods, wood and industrial raw material.
The company has maintained its operational efficiency at the best with average trailer turnaround time of 45 minutes. It has a very spacious warehouse measuring 975156.46 sq ft which enables smooth movement of goods in and out of the facility even during peak business hours. The company has total 6,915 ground slots and the average number of containers handled per day is 254 teu in exports and 726 teu in imports. Allcargo maintains swift operations with 4 RTGCs, 15 reach stackers and 58 forklifts.
Latest innovations include: introduced Six Sigma Quality Process methodology in billing and EDI documentation which helped in saving 4 minutes per transaction and enhanced customer experience. New modules have been developed in import, export & DPD for hassle-free customer experience. Multiple kiosks are provided to customers for accessing portal to check current status of containers. AEO certification from Customs, Ministry of Finance, has helped the company in saving Rs.8 lakhs p.a. A third-party payment gateway is introduced which is first of its kind in the CFS industry.
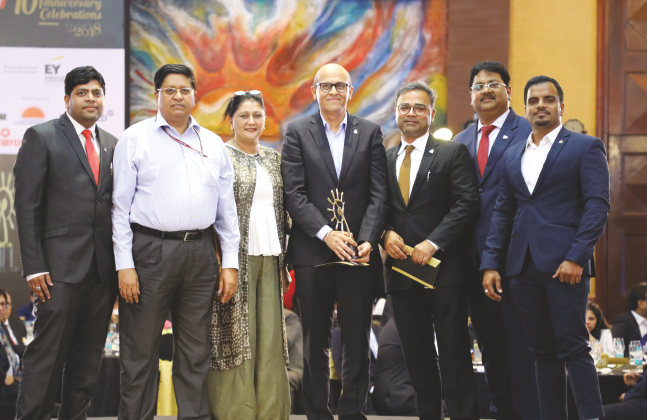
International Cargo Terminals and Infrastructure Private Ltd reported a spectacular 94,073 teus in throughput in FY2017-18, marking a growth of 10.74 per cent over FY2016-17. Major export commodities moving through the terminal include RMG, carpets and medicine, while major import commodities include chemicals, automobile parts and white goods. The operational efficiency of the terminal can be judged by the fact that it has maintained average trailer turnaround time to a minimum of 3 hours. Any growth in cargo traffic can be easily accommodated in the ample warehousing space of 5000 sq.ft. The terminal has total 853 ground slots with average number of containers handled per day standing at 241 teu for imports and 16 teu in exports.
To ensure quick movement of cargo the terminal has maintained ample infrastructure. It has seven reach stackers, while new additions of RTGC, reach stacker and forklifts have been made in FY2017-18 to accommodate the growth in traffic. As a part of its green initiative the terminal has signed a power purchase agreement based on rooftop solar power and will be operational in month of Dec-18. It will have a capacity of 500Kw. Another attraction at the CFS is the unique reefer structure constructed for reefer container monitoring: International Cargo Terminals is the only CFS to have constructed state-of-the-art reefer monitoring and plugging stacks – like port terminals. This would benefit better monitoring and safe plug in and out of reefers.
Introducing Man- Machine Interface the terminal has made a breakthrough in yard safety by introducing Man-Machine Interface. (RFID enabled jackets for yard users which send alerts when users are close to operating machines have been installed for safe operations).
Another first of its kind concept introduced is snaps of containers at the time of Gate-in: A unique blend of 3 different operating platforms is merged together to provide an automated solution. The three platforms include Fixed Camera Assembly, CFS Management System and OCR reader. An exceptional idea that would drastically reduce gate pass generation time, with proper supporting evidences.
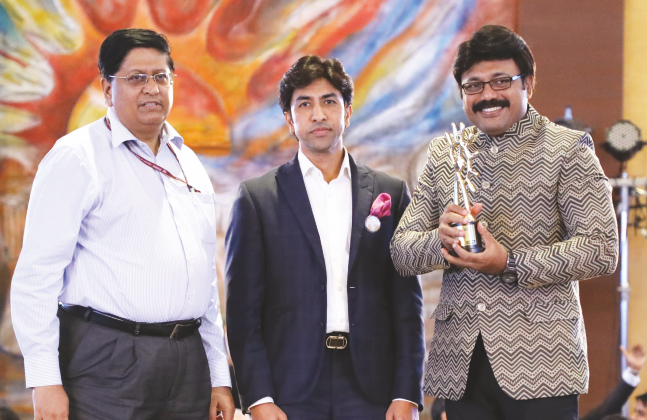
If you continue to do something for more than 30 years, you are bound to attain perfection in it. The same applies to the art of moving cargo in containers as well. It was in 1981 that the first ISO container was moved inland by the Indian Railways to India’s first Inland Container Depot (ICD) at Bangaluru, so being a pioneer in moving containerised cargo, ICD Whitefield naturally stood ahead of the crowd to be the proud recipient of the “Inland Container Depot of the Year” award.
Having moved a remarkable 167,375 teus in the assessment year 2017-18, ICD Whitefield recorded a growth rate of 10.18 per cent over the previous year FY2016-17. A major factor for the success of an ICD is its connectivity, and ICD Whitefield is connected to seven ports including -Chennai (CITPL & CCTL), Kattupalli, Krishnapatnam, Vallarpadam, Mumbai (JNPT & NSPT), Mangalore and Tuticorin.
On some of the efficiency parameters the ICD has performed exceptionally – The average trailer turnaround time (gate entry to exit) is maintained at two hours based on the traffic restrictions. With ambient warehousing space of 436,205 Sq.ft the ICD is positioned to conveniently handle movement of cargo even during peak business hours. Catering to the needs of perishable, time and temperature sensitive cargo, the ICD has cold storage space of 1000 Sq.ft. It has approximately 1,370 grids of 25 sq.ft each for cargo and approx. 9205 slots for containers.
Some of the key efficiency indicators of the ICD are: It handled 225 teu of export containers and 270 teu of import containers per day on an average, during the evaluation period. India’s containerised trade has been growing year on year, which requires infrastructure at ICDs and CFSs to be upgraded continuously. During the evaluation period, ICD Whitefield added 5 reach stackers and 15 forklifts. In March 2018, the operational old reach stackers were replaced with brand new machines. Rs.8 crores have been invested for creating better roads for moving trailer traffic, creation of parking space for the trailers, CC block paving in and around the warehouses to make it ambient as well for easing the forklift operations.
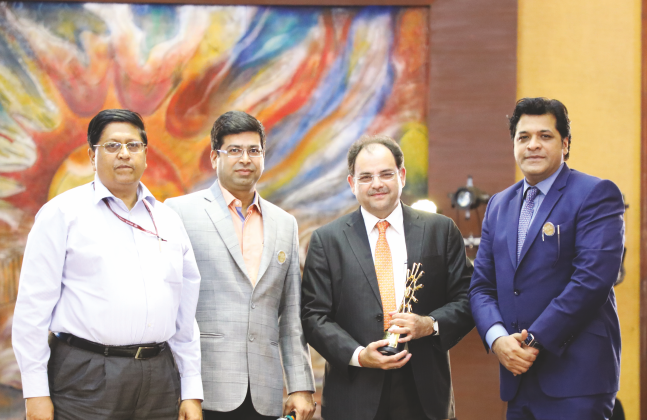
The motto of Samsara Group “Success in Service” has indeed taken this dynamic shipping agency to scale new heights and be the proud recipient of ‘Shipping Agent of the Year’ award. Recognized as one of the youngest companies to establish a nationwide network of offices in a very short time, Samsara Group enjoys the enviable distinction of being a trendsetter in the industry. The company has the distinction of having added highest number of agencies of carriers to its portfolio under container, break bulk, tankers and dry bulk during the year. The largest agency network of Samsara across India spans more than 80 locations. During the evaluation period FY2017-18, Samsara Group handled 0.7 million teus of containers, 35.6 million metric tonnes of dry bulk, 1.54 million metric tonnes of break bulk and 266,560 units of Ro-Ro cargo.
The company also handled an impressive 713 bulk/tanker vessels, 103 break bulk/heavy lift vessels, 138 Ro-Ro vessels and has the distinction of having added highest number of agencies during the year. As the entire shipping and logistics world is fast catching up with digitalisation, Samsara Group has ensured to maintain its lead by installing the latest communication and information management systems. AFSYS, a very powerful ERP software, enables the local feeding of all operation critical data by branches into the central server on a real time basis.
With a service portfolio comprising shipping, rail movements, CFS, ICDs, terminals and the entire gamut of logistics, Samsara Group has created value driven customer centric solutions.
Samsara group initiated its commercial operations in India in 1996. Venturing out with a business mandate of providing highly professional and solution oriented shipping and logistics services, Samsara has today progressed to be acknowledged as one of India’s elite global logistics service providers. Samsara Group laid the foundation of its growth with a strategically planned business portfolio. With a clear motive of delivering a consistently superior service experience to its customers, Samsara has created an integrated value chain of multimodal services which ensure single window access and delivery.
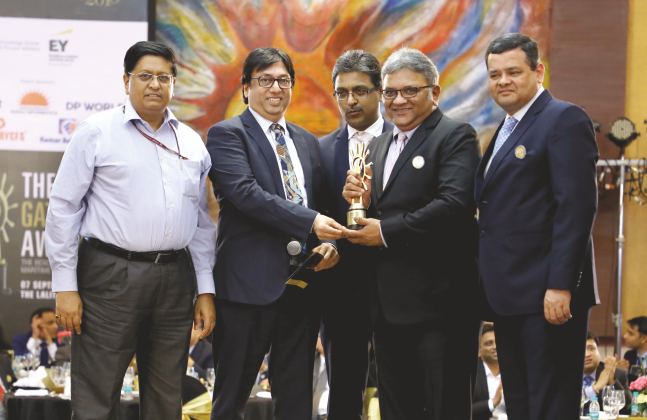
Established way back in 1917, Chinubhai Kalidass & Bros (CKB Group) is a family-owned yet very professionally run business currently managed by the third generation. The company has stood the test of times over the decades to evolve into a logistics conglomerate and proud winner of the ‘Forwarder of the Year’ award. During the evaluation period FY2017-18 the company moved 0.63 million tonnes of non-containerized cargo, while 1,17,918 teus of containerised cargo has been moved. Non-containerised cargo has grown by 14 per cent while containerised cargo has posted 10 per cent growth. Today the company has marked its presence in 785 cities across 189 countries.
The company handled 88,167 customs files, an indication of the massive business done during the evaluation period. It has a total warehousing capacity of 1,30,000 sq.ft. Some of the innovations introduced by the company include: issue of boarding pass for containers, which means once the pass is issued, loading of a container on a specific vessel is assured. Automated container tracking enables customers to track their containers till it is delivered to the consignee. In line with the current digitalisation trend in the industry, Chinubhai Kalidass & Bros has introduced fully integrated ERP system with auto updates to customers. Entire process of documentation, customer service, sales, quotations, finance is automated. Automated freight management process enables freight from carriers to be captured directly to the company’s ERP and in depth analysis with comparisons is available at the click of a button. The company is ISO 9001:2008 certified and has also achieved AEO & C-TPAT certification to enable shippers quickly move their exim cargo.
CKB Group has its reach almost all over the country with head office located in Mumbai and branch offices at locations like Ahmedabad, Baroda, Kandla, Mundra, Pipavav, Ankleshwar, Dahej, Hazira, Jaipur, New Delhi, Poona, Nagpur, Bangalore, Chennai & Tuticorin. The company also has representative offices/agents at almost all other strategic locations like Kolkata, Cochin, Ludhiana, Indore, Nasik & Kanpur.
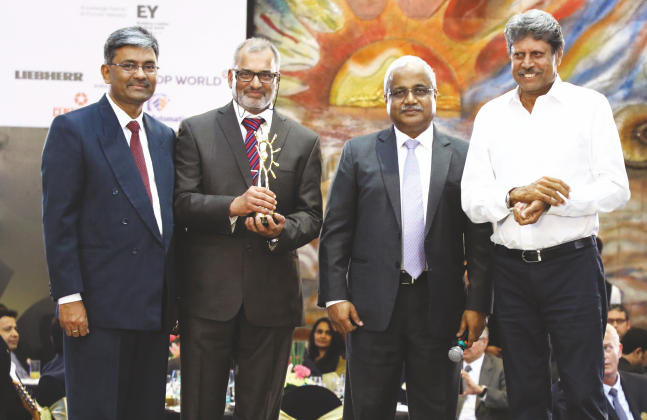
The Special Jury Award has been presented to Tolani Maritime Institute. India has a long standing tradition of producing high quality officers that serve the world’s merchant marine fleet. To a large extent this was made possible by the Indian government’s visionary initiative of establishing a few excellent maritime training institutes immediately after independence.
In recent years India’s position of leadership has been significantly weakened by an inability to keep pace with the growth in demand in terms of numbers as well as technological sophistication. Inadequate allocation of resources for maritime training from the government and lack of a suitable environment to facilitate private investment led to this decline. However, by the mid 1990’s the government had made the necessary changes to enable private initiatives in maritime training.
The Tolani Group, which has a long tradition of establishing and managing institutions of higher learning, was preparing during 1995-1997 to found a new campus-based institute that would mature into a university. As the Tolani Group’s primary business is ship owning and ship management, it was acutely aware of the need for India to produce increasing numbers of well-educated marine officers. Hence it was decided in late 1997 that the group’s new educational initiative should take the form of a modern, purpose built maritime institute.
The first degree program students at Tolani Maritime Institute were accepted in August 1998 and accommodated in temporary facilities until the new 100 acre campus was made operational in late 2000. The institute also offers internship programme and an innovative and valued component of the TMI Internship Programme is its structured and methodical approach which aims to develop on the skills and knowledge gathered by TMI students during their three years campusbased instruction. Prior to commencing the internship component of their degree programmes, each TMI student is given a Training and Resource Manual. This manual explains how the Internship Programme is structured into clearly identified sections.
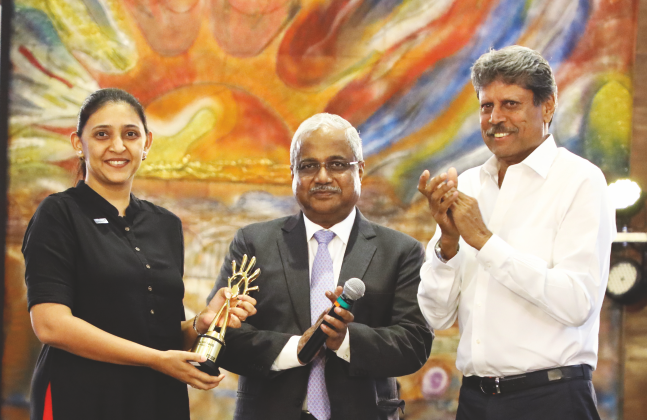
Avana Logistek Ltd has been presented the Special Jury Award. Avana Logistek Ltd was formed through the merger between Shreyas Relay Systems Ltd and Balaji Shipping Lines. Avana is a leading integrated logistics solutions provider, offering customized and end-to-end solutions to domestic and international markets. The company offers a broad spectrum of strategic and operational logistics support services to domestic and international geographical markets through seamless, energy efficient and “environment friendly” logistics solutions. Avana’s technology-enabled, “asset-light” business model allows scalability to the services it provides. Its robust streamlined business and operational processes enable to offer efficient and customized logistics solutions to customers.
The seamless connectivity Avana provides between various ports ensures integrated coverage which its customers can utilize to manage cost, time and productivity efficiencies. The company has designed its end-to-end solutions offering to offer cost advantages to customers. Recently in June 2018, Avana Logistek has filed a draft prospectus with the Securities and Exchange Board of India for an initial public offering. The IPO will comprise a fresh issue of shares for up to `300 crore ($44 million) and an offer for sale of 4.3 million shares by promoter group firm Transworld Holdings Ltd, according to a stock-exchange filing.
Avana provides coastal container services and road and rail transportation services in India. Its overseas offerings include refrigerated and dry cargo movements between the Indian sub-continent, the Middle East, Southeast Asia and the Far East, along with freight forwarding and liner agency services. Avana has also been instrumental in bringing forward the potential of coastal shipping in India.
Avana provides energy efficient and environment friendly and cost effective logistics solutions as carbon dioxide emissions from coastal shipping are minimal compared to roads and rail. The company pioneered the business of coastal container service by commencing operations in 2005 and are the largest domestic coastal logistics solutions provider.
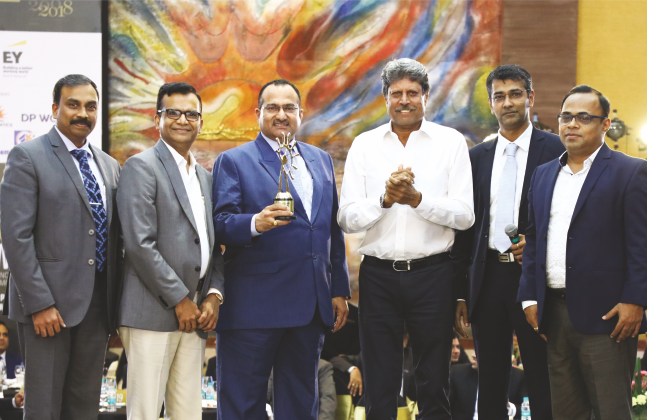
When it comes to corporate social responsibility, JSW Group through its array of initiatives has always been at the forefront with a commitment to create more smiles at every step of the group’s journey. This commitment has made the group the proud winner of ‘CSR Excellence of the Year’ award. JSW Group has allocated 2 per cent of its average net profits made during the three immediately preceding financial years towards Corporate Social Responsibility as per the categories mentioned in the Schedule VII of the Companies Act 2013. In helping local communities in skill development and employability through vocational training, the group has set up OPJ centers for vocational training. 330 local girls have been trained for non-voice BPO and fashion designing courses and 129 girls are employed at non voice BPO centre. 40 local boys are undergoing marine fitter training and spoken English training is given to 370 local boys and girls.
Women empowerment and skill development initiatives
JSW Group has always been at the forefront for women empowerment. The company has managed to help 165 women form self-help groups and engage in regular income generation programmes. Promoting entrepreneurship among women, Annapurna food stall at truck parking area is another successful model for women empowerment and employability. 6 members are earning approximately 20,000/- per month at the stall. A group of 60 women is involved in various income generation establishments like bakery products, laddu unit and preparation of traditional food items. About 25 families are engaged in preparing and selling various fish related food products.
Empowering fishermen community
To help the fishermen community an ice plant was setup in 2008 that benefits about 1700 fishermen from 5 villages. Other support for the livelihood of the fishermen such as fishing nets, out boat engine, GPS fish finder are provided by the group. Till date about 1230 fishermen from 4 villages have been benefited. Training is given to fishermen on sea safety issues.
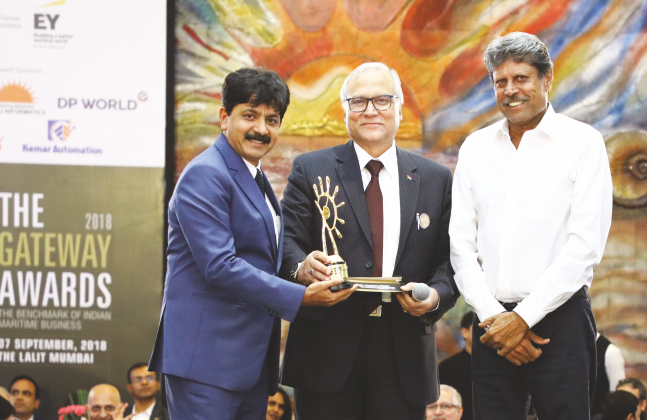
The Young Maritime Entrepreneur of the Year award has been presented to an industry leader who is also a seasoned entrepreneur with about two and half decades of experience in leading his organisation to achieve new heights.
Adarsh Hegde is the Joint Managing Director at Allcargo Logistics. He has been associated with the company since its inception. With over two and half decades of experience in the field of logistics, he has been instrumental in the success of Allcargo Logistics’ growth story. Under his leadership, Allcargo Logistics established 6 CFS & ICD facilities PAN India, making Allcargo CFS & ICD division one of the largest private players in the country. He continues to lead the blue print and strategy for the division. With his extensive experience and proficiency in transportation, he has contributed to the set-up of the Allcargo Logistics Project Forwarding division.
He is also a part of the leadership team at ECU-Line with respect to driving international procurement initiative and organisation-wide planning. After finishing his mechanical engineering from Nitte Education Trust, Mangalore, he started his career as an Assistant Maintenance Engineer with Eastern Ceramics Private Limited, Mumbai in 1987.
Among the recent developments at Allcargo Logistics is the announcement by Avvashya CCI Logistics Pvt Ltd to invest ₹400 crore by 2022 to expand its warehousing capacity to 10 million sq ft as the GST regime drives consolidation in the logistics industry. Avvashya CCI Logistics has 3.5 million sq ft of operating facility across the country and by 2022 they are looking to grow to 10 million sq ft which will require an investment of about ₹400 crore. The expansion will focus on Speciality chemicals, retail associated with e-commerce and auto engineering.
Warehouses will consolidate around major consumption centres. Guwahati is being looked at keenly by the company for expanding facilities. North-East is an area that requires high quality infrastructure and service operators with global best practices and Avvashya CCI Logistics is focusing at this region.
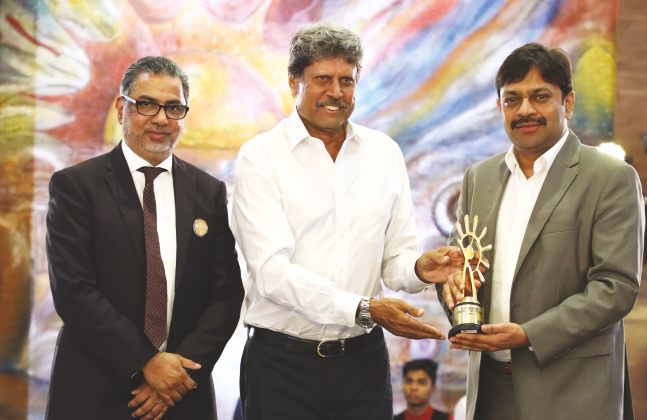
Neeraj Bansal, Chairman in-charge at JNPT, has been presented with the ‘Indian Personality of the Year’ award. He is an officer of Indian Revenue Service (IT:94) and holds a Post Graduate Degree in Law. After joining Indian Revenue Service in 1994, he worked in the Ministry of Finance in various capacities at Punjab, Haryana and Mumbai. He has more than 20 years of experience in the general managerial capacity in handling the legal, personnel, co-ordination, vigilance administrative matters.
He has vast experience of direct tax administration, investigation, tax-payer service and in formulation of tax-policy and its administration. He has handled the famous Harshad Mehta scam cases and was actively involved in the case of Vodafone India Services Pvt Ltd. He joined as Deputy Chairman at JNPT on 22nd August, 2014. The port has since then recorded a drastic improvement in its operational efficiency and business growth.
JN Port handled 66.00 million tonnes of total cargo during the financial year 2017-18. The containerized cargo was 57.87 million tonnes (87.67 per cent), liquid cargo was 7.19 million tonnes (10.89 per cent) and remaining 0.95 million tonnes (1.44 per cent) was miscellaneous types of dry bulk cargo (cement) and break bulk.
JN Port handled 4.83 million teus of container traffic during the financial year 2017-18, increased by 7.41 per cent from the previous annual container handling of 4.50 million teus during the year 2016-17. Of the total traffic of 4.83 million teus, the share of the Port operated JNPCT was 1.48 million teus (30.66 per cent), the share of NSICT was 0.64 million teus (13.26 per cent), 2.03 million teus (41.96 per cent) were contributed by M/s. Gateway Terminals India Pvt. Ltd. (APMT) i.e. APM Terminals, Mumbai, 0.66 million teus (13.64 per cent) were contributed by M/s. Nhava Sheva (India) Gateway Terminal Pvt. Ltd. (NSIGT) and remaining 0.023 million teus (0.48 per cent) were handled by newly commissioned PSA’s Terminal Bharat Mumbai Container Terminal Pvt Ltd. The container handling at JNPT constitutes about 52.91 per cent of total container traffic handled by all the Indian Major Ports (9.14 million teus).